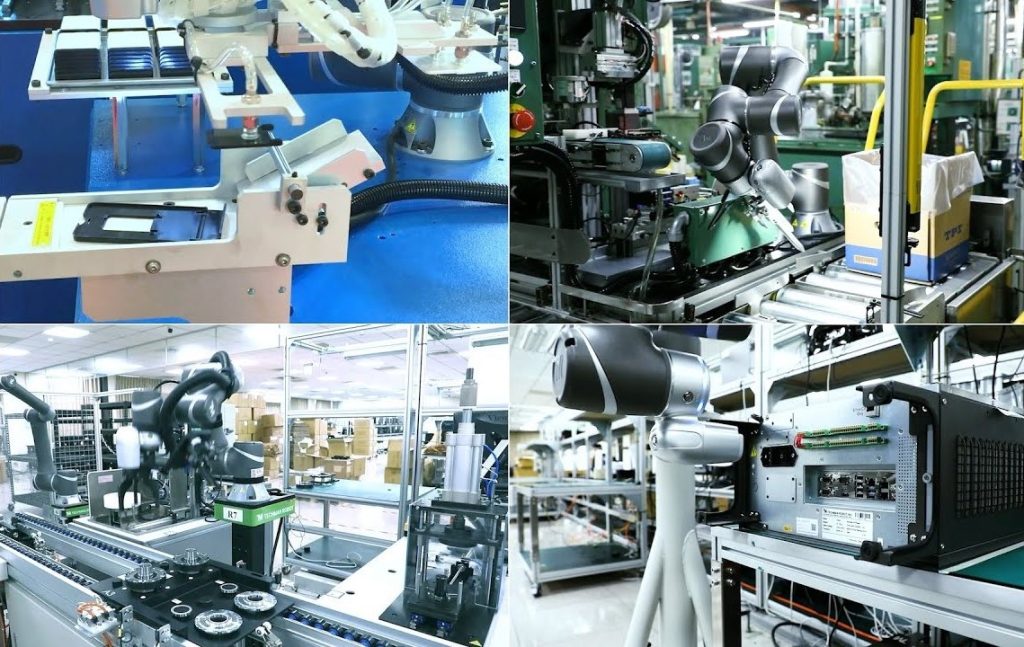
How to use a TM robot for industrial applications?
TM robots, also known as collaborative robots or cobots, are revolutionizing the industrial sector by providing automation solutions that are efficient, flexible, and cost-effective. These robots can be easily programmed and deployed in a variety of industrial applications to streamline processes, increase productivity, and improve workplace safety. In this article, we will explore how to effectively utilize a TM robot for a range of industrial applications.
1. Understand the capabilities of the TM robot:
- Before using a TM robot for industrial applications, it is essential to understand its capabilities and limitations. TM robots are designed to work alongside humans in a collaborative manner, which means they can handle tasks that are repetitive, tedious, or dangerous.
- These robots are equipped with advanced sensors and software that enable them to perform intricate tasks with precision and accuracy. They can be easily reprogrammed to adapt to different tasks and environments, making them versatile and adaptable for various industrial applications.
2. Choose the right end-effector:
- The end-effector is the tool or device attached to the robot’s arm that performs the actual work. When using a TM robot for industrial applications, it is crucial to choose the right end-effector for the specific task at hand.
- Whether it is a gripper, vacuum suction cup, welding torch, or camera, the end-effector should be selected based on factors such as the type of material being handled, the level of precision required, and the speed of operation.
3. Program the robot effectively:
- Programming a TM robot is a straightforward process that can be done using intuitive software and programming languages. By defining the robot’s movements, actions, and tasks, you can create a sequence of instructions that the robot will follow to perform the desired task.
- When programming the robot, consider factors such as the sequence of operations, motion trajectories, and safety measures to ensure smooth and efficient operation in industrial applications.
4. Integrate the TM robot into your workflow:
- Once the robot is programmed and ready for operation, it is essential to integrate it seamlessly into your existing workflow. This involves setting up the robot in the workspace, establishing communication with other machines or systems, and implementing safety measures to protect human workers.
- By integrating the TM robot into your workflow effectively, you can optimize production processes, reduce cycle times, and improve overall efficiency in industrial applications.
5. Monitor and optimize robot performance:
- After deploying a TM robot for industrial applications, it is crucial to monitor its performance and make continuous improvements to maximize its efficiency and effectiveness. This includes tracking key performance indicators, analyzing data, and making adjustments to the robot’s operation as needed.
- By monitoring and optimizing the robot’s performance, you can identify potential issues, address bottlenecks, and make informed decisions to enhance productivity and profitability in industrial applications.
In conclusion, using a TM robot for industrial applications can bring significant benefits to your business, including increased productivity, improved quality, and enhanced safety. By understanding the capabilities of the robot, choosing the right end-effector, programming effectively, integrating into your workflow, and monitoring performance, you can leverage the full potential of a TM robot to streamline processes and drive success in the industrial sector.
Was this helpful?
0 / 0