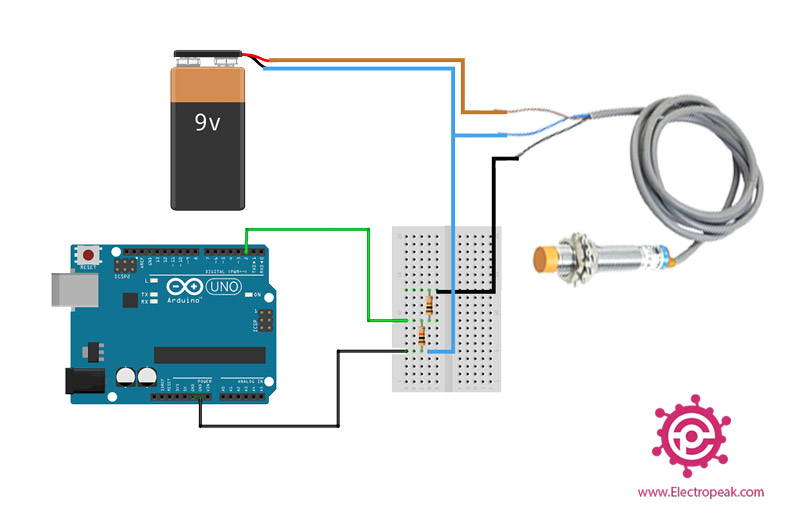
How to Interface an Inductive Proximity Sensor
Inductive proximity sensors are widely used in industrial automation applications for non-contact detection of metal objects. These sensors are reliable, durable, and easy to use. In this article, we will discuss how to interface an inductive proximity sensor with a microcontroller or PLC.
What is an Inductive Proximity Sensor?
An inductive proximity sensor is a type of sensor that detects the presence of metallic objects without physical contact. It works on the principle of electromagnetic induction. When a metallic object enters the sensing range of the sensor, it induces eddy currents in the coil, which then trigger the sensor output.
Inductive proximity sensors are available in various sizes and sensing ranges, making them suitable for a wide range of applications. They are commonly used in manufacturing, packaging, automotive, and other industries for tasks such as object detection, position sensing, and automation.
Interfacing with a Microcontroller
To interface an inductive proximity sensor with a microcontroller, you will typically need to connect the sensor’s output to one of the digital input pins of the microcontroller. The sensor output is usually an NPN or PNP transistor that switches on when a metal object is detected.
Before connecting the sensor to the microcontroller, make sure to check the sensor’s datasheet for the operating voltage and output type. You may need to add a pull-up or pull-down resistor to the sensor output pin to ensure proper signal levels.
Once the sensor is connected to the microcontroller, you can write a simple program to read the sensor output and trigger a response based on the detected object. For example, you can turn on a relay, sound an alarm, or display a message on an LCD screen.
Interfacing with a PLC
If you are interfacing an inductive proximity sensor with a programmable logic controller (PLC), the process is similar to interfacing with a microcontroller. You will need to connect the sensor output to a digital input module on the PLC and program the PLC to respond to the sensor signal.
PLCs are commonly used in industrial automation systems for controlling and monitoring machinery and processes. By interfacing the proximity sensor with a PLC, you can integrate object detection and automation functions into your PLC program.
Conclusion
Interfacing an inductive proximity sensor with a microcontroller or PLC is a straightforward process that can add value to your automation projects. By understanding the sensor’s operation and connecting it properly, you can enhance your system’s capabilities and improve efficiency.
Whether you are detecting metal objects on a conveyor belt or monitoring machine positions, an inductive proximity sensor can be a valuable tool in your automation toolkit. With the right interface and programming, you can leverage the sensor’s capabilities to enhance your industrial applications.
Was this helpful?
0 / 0