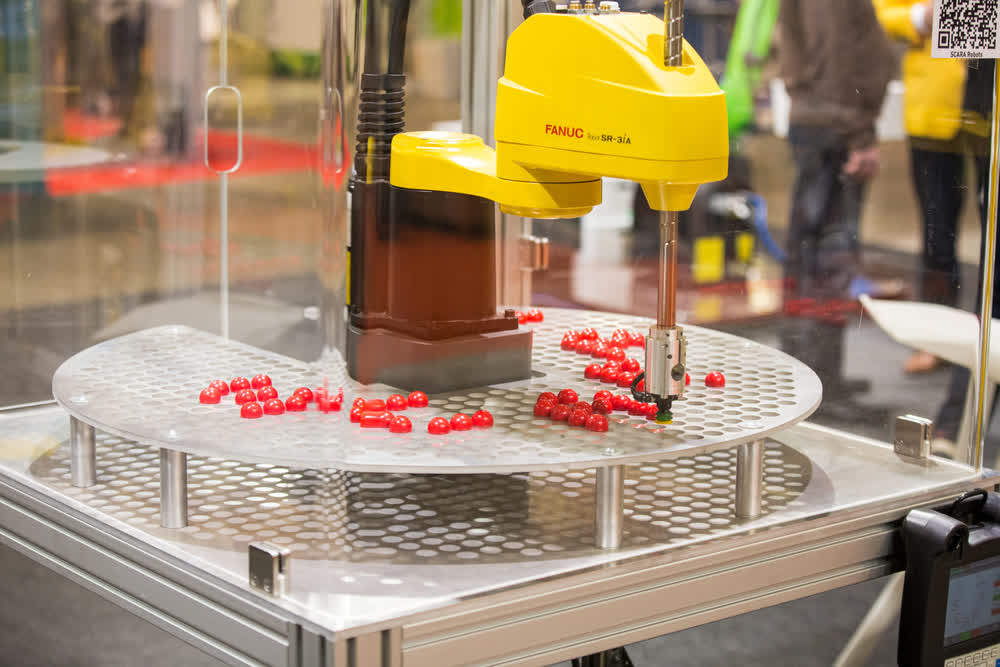
How to Configure a SCARA Robot for Precision Assembly?
SCARA robots are widely used in industrial settings for precision assembly tasks. Configuring a SCARA robot for optimal performance requires careful planning and attention to detail. In this guide, we will walk you through the process of setting up a SCARA robot for precision assembly.
1. Define Your Assembly Requirements
Before you start configuring your SCARA robot, it’s essential to define your assembly requirements. Consider the size and weight of the parts to be assembled, the required accuracy and repeatability, and the cycle time for each assembly task. This information will help you select the right SCARA robot model and configure it accordingly.
2. Select the Right End-Effector
The end-effector is a crucial component of a SCARA robot for precision assembly. Selecting the right end-effector for your application is essential to ensure accurate and efficient assembly. Consider the type of grip required, the size and weight of the parts, and any special requirements such as force sensing or vision guidance.
3. Configure Motion Parameters
Once you have selected the right SCARA robot and end-effector, it’s time to configure the motion parameters. Set the maximum speed, acceleration, and deceleration values to ensure smooth and precise movement of the robot. Adjust the path planning algorithms to minimize cycle time and optimize assembly performance.
4. Calibrate the Robot
Calibrating the SCARA robot is essential to achieve accurate and repeatable assembly results. Use a precision calibration tool to adjust the robot’s position and orientation, as well as the end-effector’s grip force and alignment. Perform regular calibration checks to maintain optimal performance over time.
5. Implement Quality Control Measures
To ensure the precision of the assembly process, implement quality control measures such as vision inspection, force sensing, and error detection algorithms. Monitor key performance indicators such as cycle time, error rate, and part rejection rate to identify and address any issues that may arise during assembly.
6. Optimize the Assembly Process
Continuously monitor and optimize the assembly process to improve efficiency and productivity. Analyze the data collected during assembly to identify areas for improvement and implement changes to enhance the overall performance of the SCARA robot. Consider integrating technologies such as machine learning and AI to further optimize the assembly process.
Conclusion
Configuring a SCARA robot for precision assembly requires careful planning and attention to detail. By following the steps outlined in this guide, you can optimize the performance of your SCARA robot and achieve accurate and efficient assembly results. Keep in mind that continuous monitoring and optimization are essential to maintaining the precision and reliability of the assembly process.
Was this helpful?
0 / 0