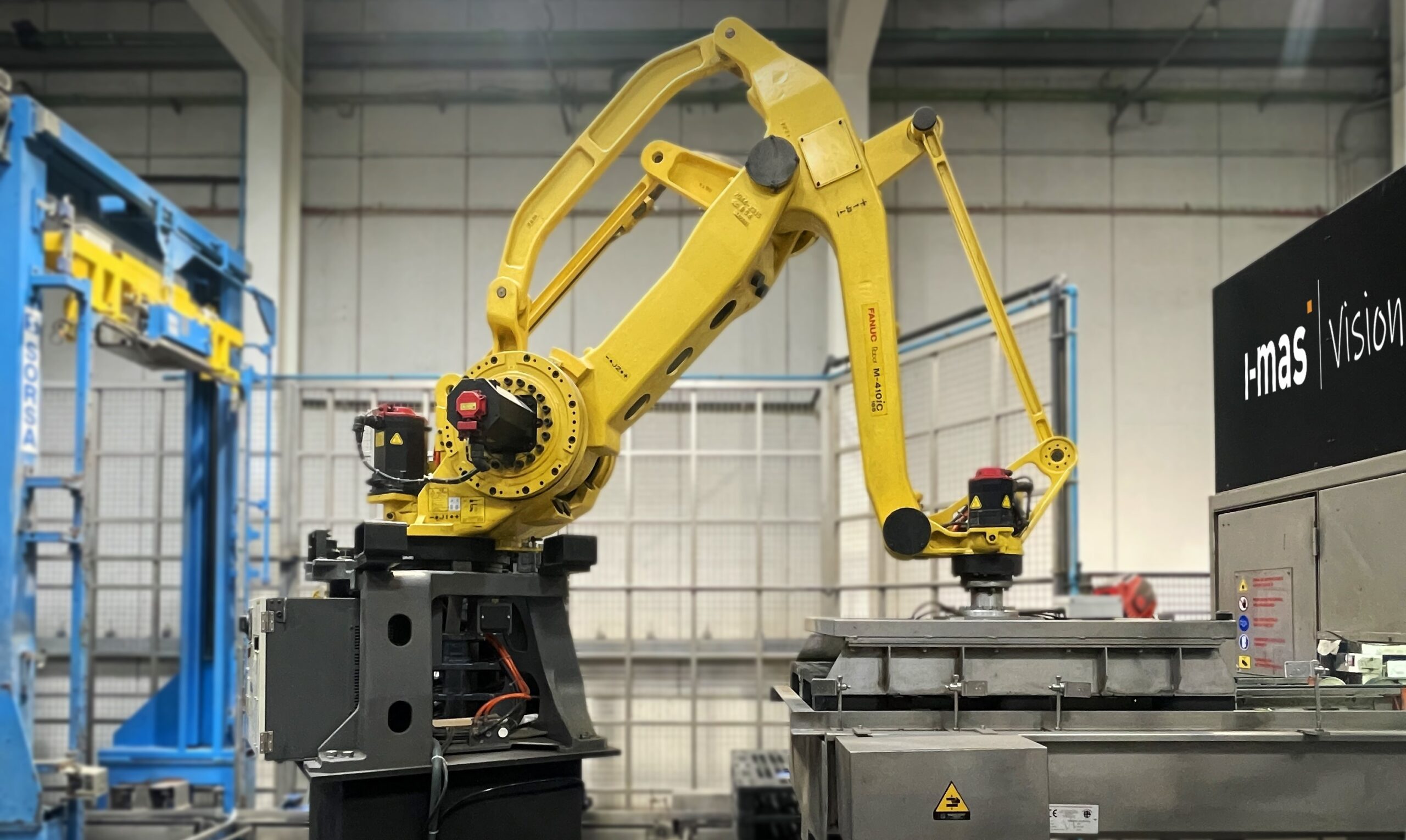
How to integrate industrial robots into production lines?
Industrial robots have revolutionized the manufacturing industry by automating repetitive tasks, increasing productivity, and improving product quality. Integrating industrial robots into production lines can be a challenging yet rewarding process. Here are some key steps to seamlessly integrate industrial robots into your production lines:
1. Assess your production needs
Before integrating industrial robots into your production lines, it is essential to assess your production needs thoroughly. Identify the tasks that can be automated and the areas where robots can add value. Consider factors such as production volume, product complexity, and safety requirements.
2. Choose the right robot for the job
There are various types of industrial robots available, each designed for specific tasks and environments. Consider factors such as payload capacity, reach, speed, and accuracy when choosing the right robot for the job. Collaborative robots (cobots) are also gaining popularity for their flexibility and ease of integration.
3. Design an efficient layout
Designing an efficient layout for your production lines is crucial for seamless robot integration. Consider factors such as workspace optimization, safety barriers, and ergonomic considerations. Ensure that the robot can move freely and safely within the production environment.
4. Integrate robot control systems
Integrating robot control systems with your existing production systems is essential for smooth operation. Ensure that the robot can communicate effectively with other machines, sensors, and PLCs. Use industry-standard communication protocols such as Ethernet/IP or Profinet for seamless integration.
5. Provide comprehensive training
Training your employees on how to operate, maintain, and troubleshoot industrial robots is essential for successful integration. Ensure that your team is familiar with the robot’s programming interface, safety procedures, and emergency stop protocols. Regular training sessions can help improve efficiency and reduce downtime.
6. Conduct thorough testing and validation
Before fully integrating industrial robots into your production lines, conduct thorough testing and validation to ensure that the robots perform as expected. Test different scenarios, such as varying production volumes and product variants, to identify any potential issues and fine-tune the robot’s performance.
7. Monitor and optimize performance
Once industrial robots are integrated into your production lines, continuously monitor and optimize their performance. Collect data on cycle times, error rates, and overall equipment effectiveness (OEE) to identify areas for improvement. Regular maintenance and software updates can help maximize productivity and minimize downtime.
By following these steps and leveraging the latest technologies, you can seamlessly integrate industrial robots into your production lines and improve efficiency, flexibility, and competitiveness in the manufacturing industry.
Was this helpful?
0 / 0