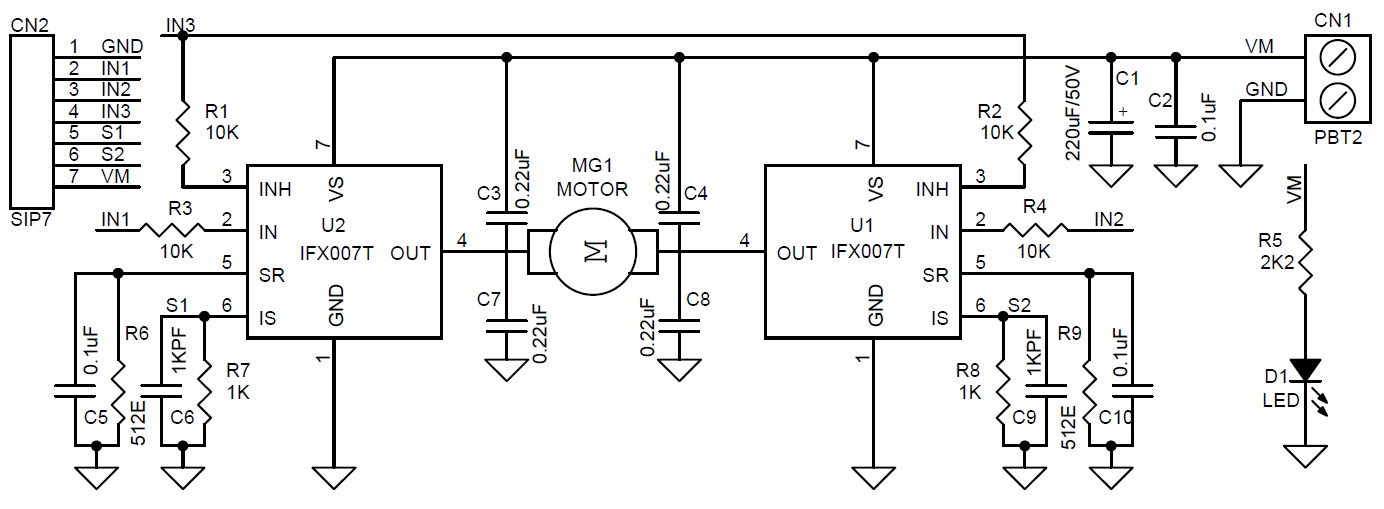
How to Design a High-Power DC Motor Driver Circuit
Designing a high-power DC motor driver circuit can be a complex but rewarding process. Whether you are building a robot, a CNC machine, or any other project that requires precise motor control, having a solid driver circuit is crucial. In this guide, we will walk you through the steps of designing a high-power DC motor driver circuit from scratch.
Step 1: Determine Your Motor Specifications
The first step in designing a motor driver circuit is to determine the specifications of your DC motor. You will need to know the voltage and current rating of your motor, as well as any other relevant information such as the stall current and speed. This information will help you select the appropriate components for your driver circuit.
Step 2: Choose the Right Components
Once you have determined the specifications of your motor, you can start selecting the components for your driver circuit. Key components to consider include MOSFETs, gate drivers, current sense resistors, and flyback diodes. Make sure to choose components that can handle the voltage and current requirements of your motor.
Step 3: Design the Driver Circuit
With your components selected, it’s time to design the actual driver circuit. You will need to create a schematic diagram that shows how all the components are connected together. Pay close attention to the wiring of the MOSFETs, as incorrect wiring can lead to inefficiencies and even damage to the components.
Step 4: Test and Debug
Once you have built your driver circuit, it’s essential to test and debug it thoroughly. Connect your motor to the driver circuit and check that it operates as expected. Use an oscilloscope to monitor the voltage and current waveforms, and make any necessary adjustments to ensure smooth and efficient motor control.
Step 5: Optimize for Efficiency
After testing your driver circuit, you may want to optimize it for efficiency. This can involve adjusting component values, fine-tuning the control algorithm, or even using more advanced control techniques such as PWM. By optimizing your driver circuit, you can improve the performance and longevity of your DC motor.
Step 6: Consider Safety Precautions
When designing a high-power DC motor driver circuit, it’s crucial to consider safety precautions. Make sure to include overcurrent protection, thermal protection, and any other safety features that are relevant to your application. Safety should always be a top priority when working with high-power electronics.
Conclusion
Designing a high-power DC motor driver circuit requires careful planning, attention to detail, and a solid understanding of electronics. By following the steps outlined in this guide, you can create a reliable and efficient driver circuit for your motor control project. Remember to test your circuit thoroughly, optimize it for efficiency, and always prioritize safety in your design.
Was this helpful?
0 / 0