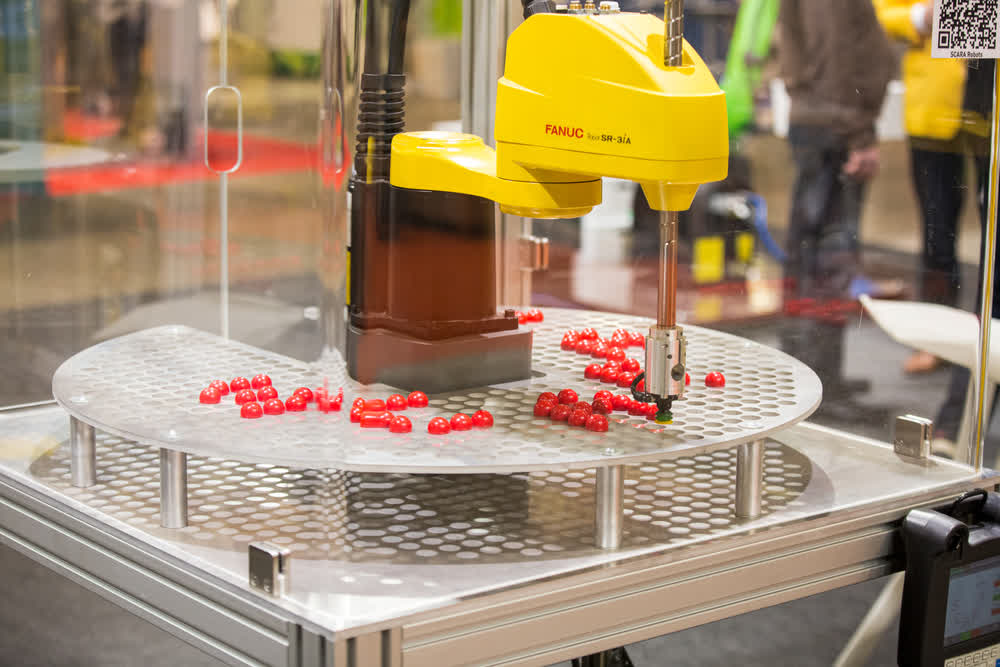
How to configure a SCARA robot for precision assembly?
When it comes to precision assembly in manufacturing, SCARA robots are widely used for their speed, flexibility, and accuracy. These robots are ideal for tasks that require repetitive movements with high precision, making them essential in industries such as electronics, automotive, and medical devices.
1. Selecting the right SCARA robot model
Before you can configure a SCARA robot for precision assembly, you need to consider the specific requirements of your manufacturing process. Factors such as payload capacity, reach, speed, and accuracy will all play a role in determining the right SCARA robot model for your needs.
- Assess the payload capacity needed for your assembly tasks.
- Determine the reach required to access all areas of the work envelope.
- Consider the speed and accuracy required to meet production goals.
- Choose a SCARA robot model that meets these requirements within your budget.
2. Setting up the SCARA robot workspace
Once you have selected the right SCARA robot model, the next step is to set up the workspace for precision assembly. This includes configuring the robot’s end-effector, camera systems, sensors, and any other peripherals needed for your specific tasks.
- Mount the SCARA robot securely to the work surface.
- Calibrate the robot’s end-effector to ensure precise movements.
- Install any necessary cameras or sensors for feedback control.
- Program the robot’s motion and logic controllers for assembly tasks.
3. Programming the SCARA robot for precision assembly
Programming a SCARA robot for precision assembly requires a detailed understanding of the robot’s capabilities and the specific requirements of your manufacturing process. You will need to create motion profiles, logic sequences, and error-handling routines to ensure smooth operation and high-quality output.
- Use the robot’s programming software to create motion paths for assembly tasks.
- Implement logic sequences to control the robot’s movements and actions.
- Test the program thoroughly to identify and correct any errors or issues.
- Optimize the program for speed, accuracy, and repeatability.
4. Fine-tuning the SCARA robot for optimal performance
Once you have programmed the SCARA robot for precision assembly, it is important to fine-tune its performance to ensure the highest level of accuracy and efficiency. This may involve adjusting parameters such as acceleration, deceleration, and tool offsets to optimize the robot’s movements.
- Use the robot’s built-in diagnostic tools to monitor performance and identify areas for improvement.
- Make adjustments to the robot’s settings to fine-tune its performance for specific tasks.
- Regularly check and maintain the robot’s components to ensure optimal operation.
- Continuously optimize the robot’s program and settings to improve efficiency and quality.
By following these steps, you can successfully configure a SCARA robot for precision assembly and optimize your manufacturing process for maximum productivity and quality.
Was this helpful?
0 / 0